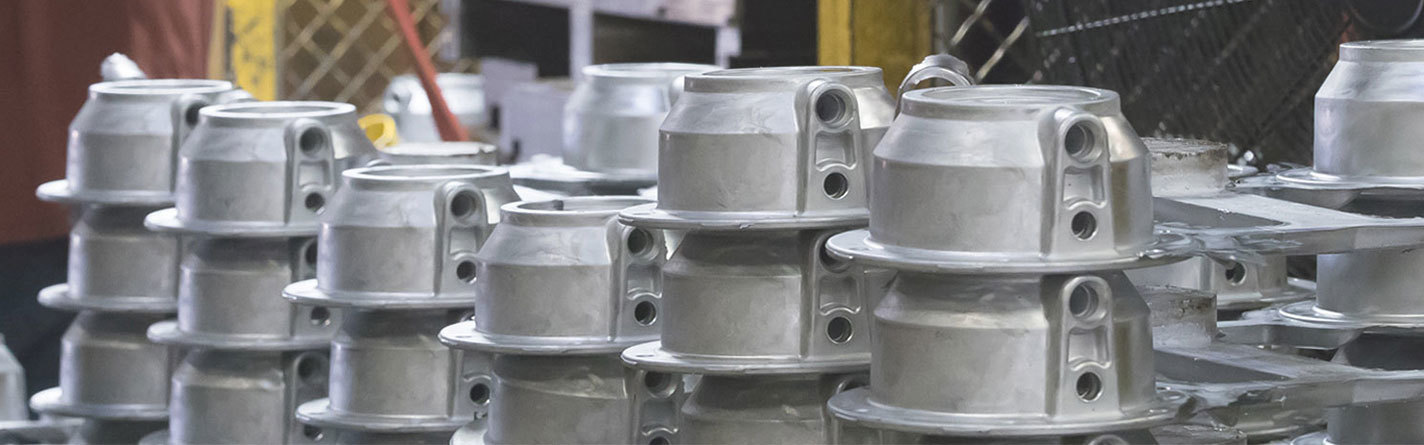
低压压铸
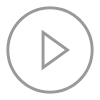
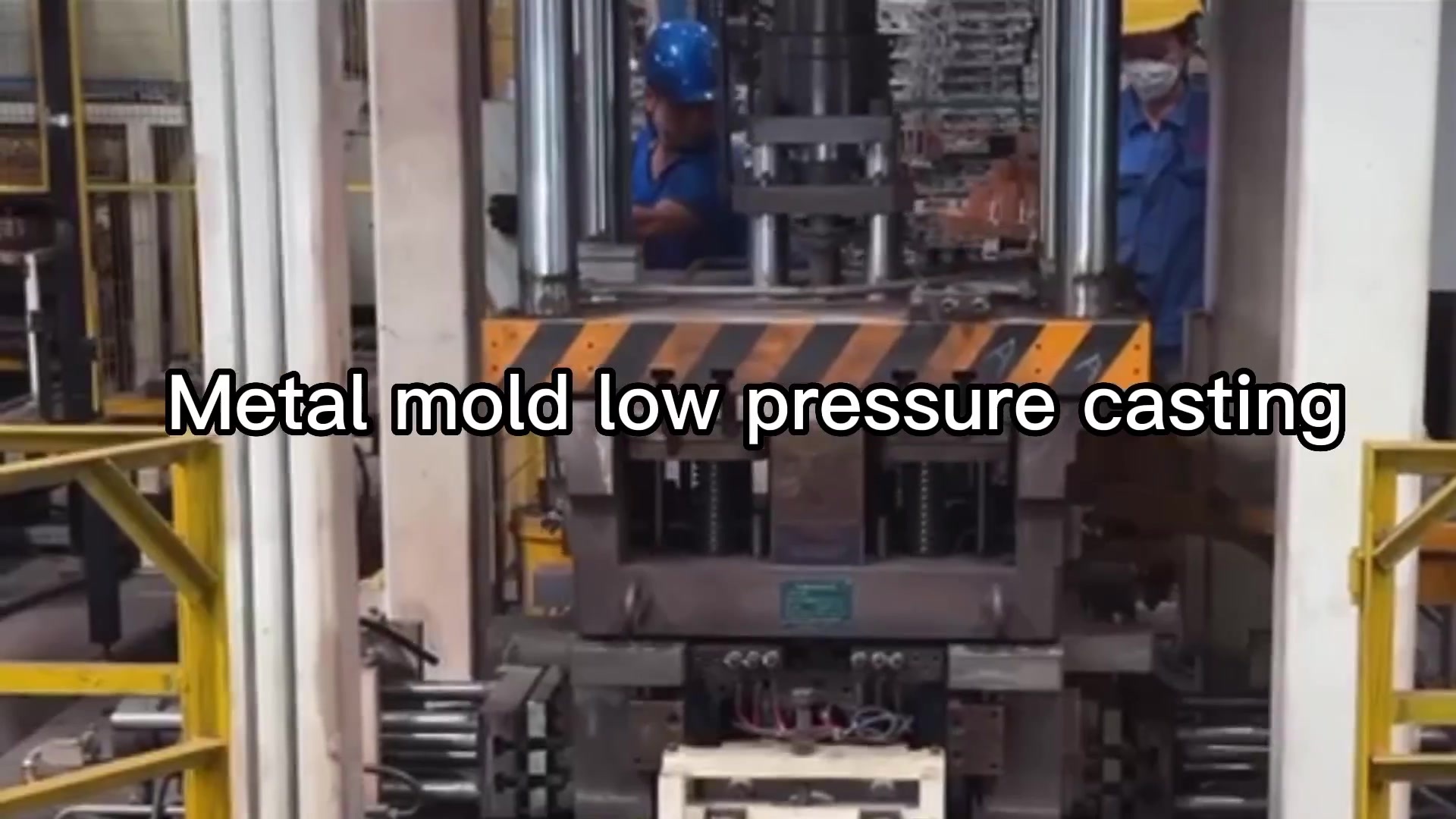
什么是低压压铸?
- 低压压铸材质
材质 | 牌号 | 特点 |
铝合金 | A356 | 机械性能良好 耐腐蚀 易于加工 |
A380 | 强度高 流动性好 适合复杂形状 | |
A360 | 抗拉强度更高 延展性好 | |
镁合金 | AZ91D | 优异的比强度和刚度 重量轻 耐腐蚀性好 |
AM60B | 延展性更高 抗冲击性好 | |
锌合金 | ZAMAK 3 | 流动性好,表面光洁度高 性价比高 |
ZAMAK 5 | 强度和硬度较高 耐腐蚀性好 | |
铜合金 | 黄铜(C26000) | 良好的导电性和导热性 良好的可加工性 |
青铜(C95500) | 强度高、耐磨 耐腐蚀性能好 |
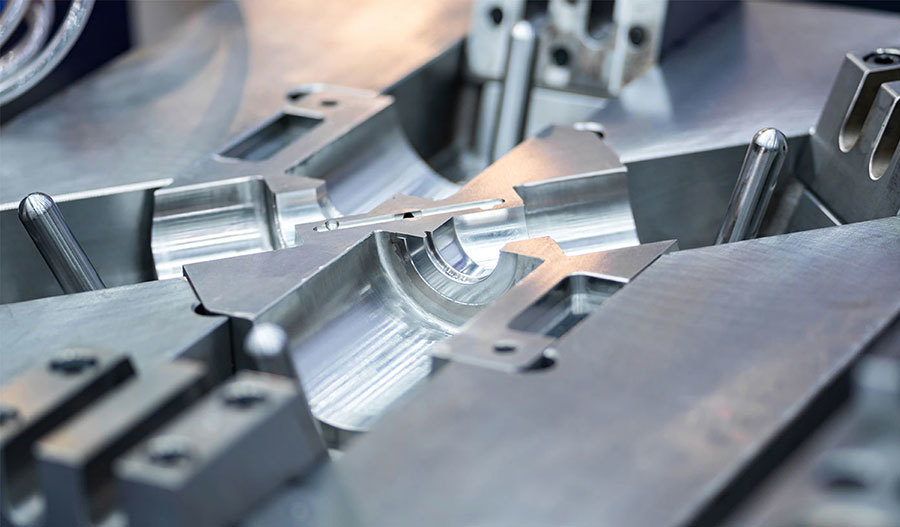
低压压铸流程
1. 准备模具
● 模具设计:根据所需零件的设计,制作模具。模具通常由耐高温的材料制成,如钢或石墨。
● 模具预热:将模具加热到适当的温度,以减少热应力和提高金属流动性。
2. 装载熔融金属
● 熔化金属:将铝合金或其他轻合金放入熔炉中熔化,确保金属完全熔化且温度均匀。
● 除气和除渣:通过添加除气剂和除渣剂,去除熔融金属中的气体和杂质,提高金属的纯净度。
3. 预热浇注系统
● 预热浇道:将浇注系统的浇道和浇口预热至适当温度,以确保熔融金属流动顺畅。
4. 浇注
● 低压充型:将熔融金属通过一个密封的管道引入模具底部。通过施加低压(通常为0.02至0.07 MPa),使金属缓慢上升并充满模具腔。
● 压力保持:在金属完全凝固之前,保持一定的压力,以确保金属充分填充模具并补偿收缩。
5. 冷却和凝固
● 冷却:控制冷却速度,使金属在模具内均匀凝固。冷却速度可以通过调节模具温度和冷却介质来控制。
● 凝固:确保金属完全凝固,形成所需的形状和结构。
6. 开模取件
● 开模:当铸件完全凝固后,打开模具,取出铸件。
● 清理:去除浇道、冒口和其他多余的金属部分,清理铸件表面。
7. 后处理
● 检查:对铸件进行外观和尺寸检查,确保符合质量标准。
● 热处理:根据需要,对铸件进行热处理,以改善其机械性能。
● 表面处理:进行必要的表面处理,如打磨、抛光、涂漆或电镀,以达到最终的表面质量和防腐性能。
8. 检验和包装
● 最终检验:对成品进行最终的质量检验,确保所有参数符合客户要求。
● 包装:将合格的铸件进行包装,准备发货。
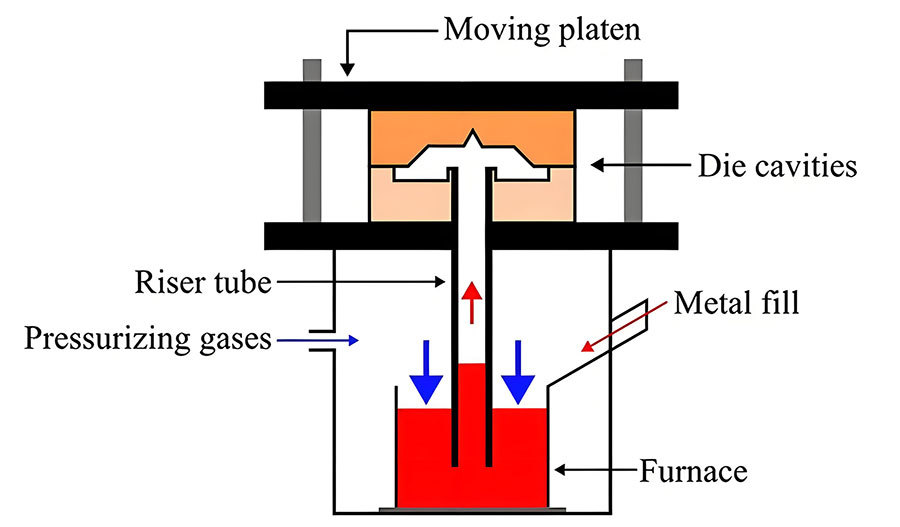
低压压铸应用
低压压铸是一种高效的铸造技术,特别适合生产高质量、尺寸精确且形状复杂的金属零件。该技术应用范围很广,特别是在汽车工业和其他需要精密铸件的领域。以下是低压压铸的主要应用:
行业 | 应用 |
汽车 | 生产车轮、发动机零部件、制动系统零部件、悬架系统零部件。 |
航空航天 | 制造飞机和航天器的结构和功能部件。 |
电子产品 | 为电子设备创建外壳和内部支撑结构。 |
机械 | 生产泵体、阀体等机械零件。 |
消费品 | 生产运动器材和家用电器的零部件。 |
可再生能源 | 用于电动汽车电池盒的生产。 |
低压压铸优缺点
- 低压压铸优点
1. 高质量铸件
● 表面光洁度高:低压压铸可以生产出表面光洁度高的铸件,通常可达125微英寸Ra(3.175微米Ra)
● 内部缺陷少:由于低压充型过程较为平缓,减少了气孔、夹杂和裂纹等内部缺陷。
1. 高质量铸件:
● 表面光洁度高:低压压铸可以生产出表面光洁度高的铸件,通常可达125微英寸Ra(3.175微米Ra)。
● 内部缺陷少:由于低压充型过程较为平缓,减少了气孔、夹杂和裂纹等内部缺陷。
2. 高精度:
● 紧公差:低压压铸可以实现非常严格的尺寸公差,通常可达±0.005英寸(±0.127毫米)。
● 一致性好:生产出的铸件尺寸稳定,一致性高,适合批量生产。
3. 材料利用率高:
● 减少飞边和废料:由于低压充型过程较为平缓,减少了飞边和多余的金属,提高了材料利用率。
● 废品率低:高质量的铸件减少了废品率,降低了生产成本。
4. 适用范围广:
● 复杂形状:低压压铸可以生产形状复杂、壁厚较薄的零件,适用于各种复杂设计。
● 轻合金:特别适合生产铝合金和其他轻合金的零件,广泛应用于汽车、航空航天等领域。
5. 环保:
● 废料少:低压压铸过程中产生的废料较少,对环境的影响较小。
● 能源消耗低:相对于高压压铸,低压压铸的能耗较低,更加节能环保。
6. 生产效率高:
● 自动化程度高:低压压铸可以实现高度自动化,提高生产效率和劳动生产率。
● 周期短:生产周期相对较短,适合大规模生产。
7. 力学性能好:
● 均匀的微观结构:低压压铸可以产生均匀的微观结构,提高铸件的力学性能。
● 高强度和韧性:铸件具有较高的强度和韧性,适合承受高负荷的应用。
8. 热处理和表面处理容易:
● 热处理:低压压铸的铸件易于进行热处理,以改善其机械性能。
● 表面处理:铸件表面光洁,易于进行打磨、抛光、涂漆或电镀等表面处理。
9. 模具寿命长:
● 模具磨损小:由于低压充型过程较为平缓,模具受到的冲击和磨损较小,延长了模具的使用寿命。
10. 灵活性高:
● 设计变更容易:低压压铸模具相对简单,设计变更较为容易,适合快速响应市场需求。
- 低压压铸缺点
1.生产速度较慢:
● 充型速度慢:低压压铸采用较低的压力,导致金属充型速度较慢,生产周期较长。
● 生产效率低:相对于高压压铸,低压压铸的生产效率较低,不适合需要极高产量的生产环境。
2. 初始投资成本高:
● 设备成本高:低压压铸设备的初始投资成本较高,包括模具、熔炼设备和控制系统等。
● 模具成本高:低压压铸模具通常需要更高的精度和耐用性,因此成本较高。
3. 适用材料有限:
● 主要适用于轻合金:低压压铸主要适用于铝合金和其他轻合金,对于某些重合金或特殊合金的适用性较差。
● 材料限制:不适合生产需要极高强度和耐高温的材料。
4. 铸件壁厚限制:
● 壁厚要求:低压压铸更适合生产壁厚较均匀的零件,对于壁厚差异较大的零件可能难以保证质量和充型效果。
● 薄壁件难度大:虽然低压压铸可以生产薄壁件,但对于极薄壁件(如壁厚小于1mm)的生产仍有一定难度。
5. 模具维护成本高:
● 模具寿命:尽管低压压铸对模具的冲击较小,但模具仍需定期维护和修复,增加了维护成本。
● 复杂模具:对于复杂形状的模具,维护和修复工作更为复杂和昂贵。
6. 工艺控制要求高:
● 温度控制:低压压铸对熔融金属的温度控制要求较高,需要精确的温度监控和调整。
● 压力控制:充型压力的控制也需要精确,以确保铸件质量和一致性。
7. 设备占地面积大:
● 空间需求:低压压铸设备通常较大,需要更多的车间空间,对于空间有限的生产环境可能不太适合。
8. 生产灵活性较低:
● 模具更换时间长:低压压铸模具更换和调试时间较长,生产灵活性较低,不适合频繁更换产品类型的小批量生产。
9. 表面处理要求高:
● 表面质量:虽然低压压铸可以生产表面光洁度高的铸件,但在某些情况下仍需要额外的表面处理,如打磨、抛光等,增加了后续加工成本。
我们很乐意与您联系
我们将在一个工作日内联系您。请注意您的电子邮件。